When cold waves strike strawberry orchards in southern China, farmers light smoking stoves overnight but still struggle to prevent crop frost; when heavy rains collapse northern greenhouses, strawberry seedlings rot in standing water—traditional open-field cultivation and greenhouse agriculture remain bound by the spell of "relying on the weather for harvest." Data shows annual yield reduction due to extreme climates in China’s main strawberry producing areas reaches 15%–20%, while transportation loss rates soar to 30%, turning the "last mile" from field to table into a risky journey.
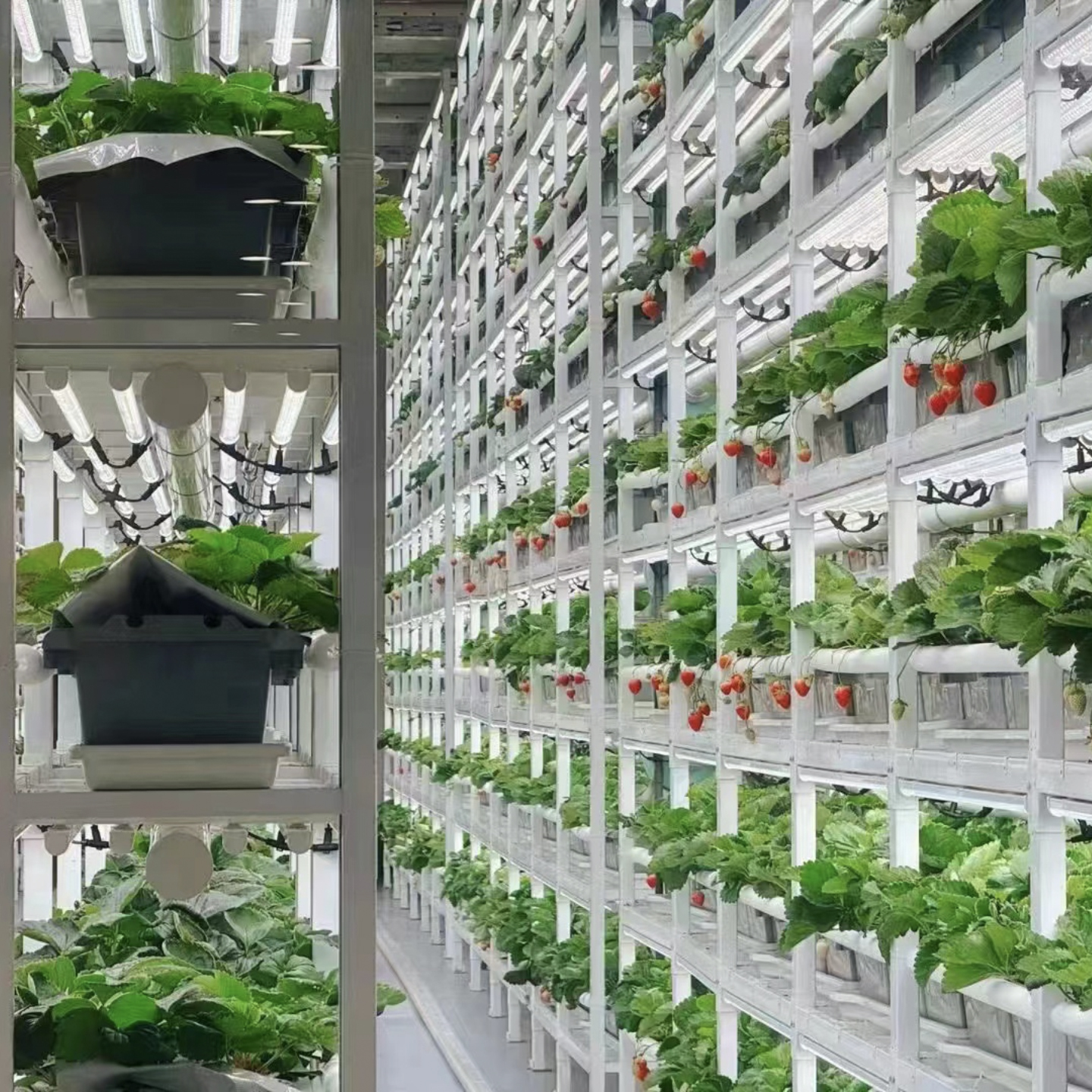
Land resource constraints are equally severe. During urbanization, suburban farmland is continuously eroded, while traditional strawberry cultivation costs over 20,000 RMB per mu and requires at least three years of crop rotation fallow. The contradiction between efficiency and cost grows increasingly acute. How to break through climate barriers and shake off land constraints has become an urgent proposition for modern agriculture.
Auma’s Strawberry Container Plant Factory creates a "climate-immune cabin" with cold storage–grade construction (thermal conductivity <0.03W/(m·K)). In the –40°C extreme cold of Hulunbuir, Inner Mongolia, the interior maintains a constant 21±5°C; at 4500m altitude in Tibet, where open-field plants stop growing due to low air pressure, "Hongyan" and "Zhangji" strawberries thrive under customized lighting.
Unlike bulky fixed greenhouses, Auma containers adopt modular design, enabling global transportation via sea, land, or even integrated hoisting. During a typhoon season, a Shanghai fresh produce chain urgently relocated 3 units to Zhoushan Islands, completing water-electricity connection and system debugging within 72 hours. While surrounding farmers suffered heavy losses, strawberries in the containers entered the harvest period as scheduled. This plug-and-play feature realizes "zero-distance freshness" in scenarios like urban suburban picking gardens and temporary planting sites near supermarkets.
Inside the 12.15m-long container, 16 sets of vertical cultivation racks stack like skyscrapers, with 192 customized LED plant lights illuminating from above. This vertical planting model allows 1,040 strawberry plants to grow "stereoscopically" on just 28 square meters, yielding 0.25 tons monthly and 3 tons annually—equivalent to the annual output of 10 mu in traditional greenhouses, with space utilization improved by 40 times. After introducing 5 units, a Shenzhen urban agriculture park meets the high-end strawberry demand of 3 surrounding communities with less than 200 square meters.
Entering the operation area, a 39-inch intelligent data dashboard real-time displays 12 core indicators like temperature, humidity, and CO₂ concentration. The PLC control system acts as the plant’s "digital brain": when sensors detect humidity exceeding 70%, the 680W dehumidifier activates automatically; when CO₂ concentration drops below 800ppm, dedicated equipment releases gas for supplementation. This temperature control precise to ±1℃ and humidity regulation to ±5% keeps strawberries in the "comfort zone," reducing disease rates by 50% compared to traditional cultivation.
The drip irrigation system and automatic fertilizer adjuster form the strawberry’s "intelligent restaurant." During the seedling stage, the system automatically mixes high-nitrogen nutrient solution; during the fruit expansion stage, it switches to a high-potassium formula. Water supply per plant is controlled at 200–300ml daily, with an error of less than 5ml. The RO reverse osmosis water filtration equipment purifies water to an EC <0.5ms/cm before delivering it to the roots via drip irrigation belts. This "personalized" water-fertilizer plan increases strawberry sweetness by 2–3 degrees on average compared to open-field cultivation.
The 180W ozone disinfection machine starts regularly, forming an invisible sterilization net in the cultivation area that controls airborne pathogen counts below 10CFU/m³. A comparative test by an organic farm owner shows that after using Auma equipment, the incidence of strawberry gray mold and powdery mildew decreases by 90%, with annual pesticide use reduced by 85%, fully meeting EU organic certification standards.
In Auma containers, strawberries complete their entire life cycle from "birth" to "maturity." Sown seedlings enjoy 16 hours of precise lighting in the seedling area and can be transplanted to cultivation racks within 25 days; during the fruit expansion period, the system adjusts the red-blue light spectrum ratio to promote anthocyanin synthesis for uniform coloring; when the refractometer detects soluble solids exceeding 12%, a harvest reminder pops up automatically. A Beijing agricultural research institute found that the stable environment in containers shortens the strawberry growth cycle by 15–20 days compared to open fields, with single-fruit weight consistency reaching 95%.
A high-end residential area in Shanghai transformed 3 Auma containers into a "community strawberry workshop," allowing residents to make picking appointments via a mobile app. From picking to consumption takes less than 2 hours. This "farm at the doorstep" model solves the pain point of long driving distances for traditional picking gardens while enabling urban children to witness plant growth directly, receiving over 200 parent-child families on weekends.
At a research station on the edge of the Taklamakan Desert in Xinjiang, Auma equipment provides fresh strawberries for researchers; in Yushu, Qinghai, at 4200m altitude, strawberries in containers become a "vitamin supply station" for local school cafeterias. The person in charge of a Tibet aid project remarked: "In the past, eating local strawberries on the plateau was a luxury. Now we harvest every week, and children no longer have to rely on canned fruits."
A Yunnan cross-border trader converted Auma containers into "strawberry-themed trucks" shuttling between Sino-Myanmar border ports. The built-in intelligent system ensures strawberries continue growing during transportation, reaching the optimal harvest period upon arrival at the port, reducing losses by 40% compared to traditional transportation. A single unit generates an annual trade volume of over 800,000 RMB.
A single Auma unit is priced at approximately 350,000 RMB, including 16 sets of cultivation racks, intelligent control systems, and full sets of environmental equipment. With a monthly output of 0.25 tons, at a high-end market price of 80 RMB/kg, monthly sales reach 20,000 RMB. After deducting approximately 5,000 RMB in water-electricity and nutrient solution costs, annual net profit reaches 180,000 RMB, with a static investment payback period of about 20 months. A agricultural cooperative that introduced 10 units now earns over 1.8 million RMB annually, driving employment for 20 rural households.
Container cultivation uses soilless cultivation substrates, eliminating the need for crop rotation fallow, with equipment lifespan exceeding 10 years. The 50,000-hour LED light lifespan means replacement is needed only after 5–6 years. Compared to the tedious tasks of replacing films and soil disinfection in traditional greenhouses, maintenance costs are reduced by 60%. A Jiangsu agricultural enterprise calculated that the annual maintenance cost for 5 units is only 12,000 RMB, less than one-third of traditional cultivation.
As Auma strawberry containers take root across the country, we see not just a planting technology but a revolution in agricultural paradigms. It frees "farmland" from soil constraints, liberates "harvest" from seasonal limitations, and breaks the geographical boundaries of "freshness." An agricultural expert has predicted: "These mobile, intelligent agricultural units will future become like 'agricultural building blocks,' constructing a globally connected 'food network' on city rooftops, desert outposts, and polar research stations."
At this moment, in a container somewhere in the city, a strawberry is absorbing precisely balanced nutrient solution, stretching its leaves under LED lights—its ripening countdown is determined by a chip, not the seasons. This may well be the most beautiful vision of modern agriculture: where technology and nature shake hands, and efficiency and quality coexist in perfect harmony.